Web cleaning is a crucial technology employed across various industrial processes such as printing, coating, laminating, and converting to ensure the quality and cleanliness of continuous rolls or webs of materials. This intricate procedure involves the removal of contaminants and unwanted substances that can compromise the final product’s quality.
In this article, we will explore the world of web cleaning, exploring common contaminants, the methods by which they reach the web material, and the benefits of effective dust removal. Furthermore, we will introduce you to the two primary types of web cleaning solutions: contact and non-contact, offering insights into their advantages and applications.
Read on to Learn
- Everything you need to know about web cleaning
- What contaminants are common in different industries
- More about the different types of web cleaning
- What web cleaning solution is best for your specific situation
What Is Web Cleaning?
Web cleaning is a process that involves removing contaminants or unwanted substances from a continuous web of material as it moves through various industrial processes. The process is common in industrial applications such as printing, coating, laminating, or converting where a continuous roll or web of material undergoes multiple treatments. Examples of materials used in these industries are packaging, paper-, solid board and corrugated production, medical.
The purpose of web cleaning is to help ensure the quality and consistency of the final product and reduce the need for machinery maintenance in these industries. Web cleaning also helps with providing a clean and safe work environment that protects the health of personnel.
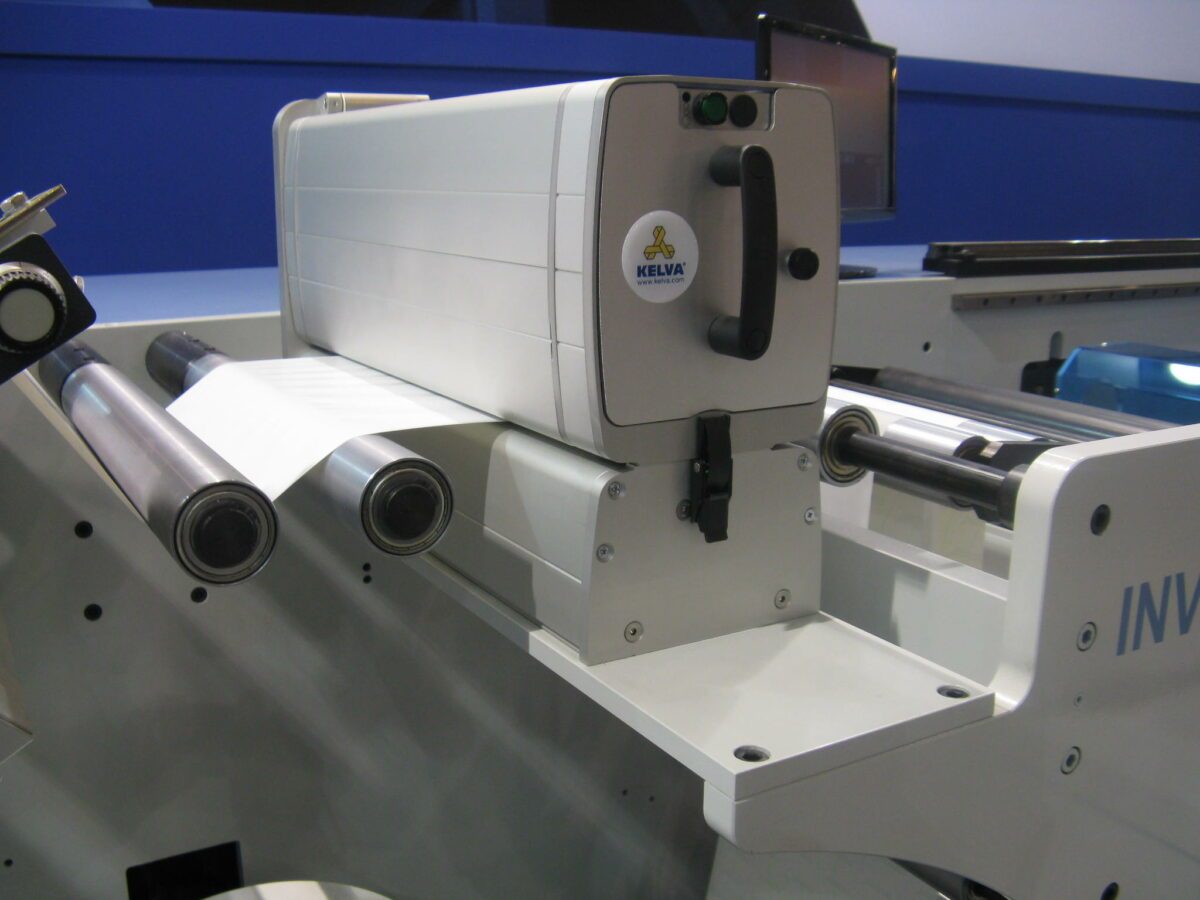
What Are Some of the Common Contaminants?
There are different types of contaminants that can reduce the quality of the production and end products in any industry. However, there are some types of contaminants that are more common than others. Examples of these common contaminants are:
Dust and Debris
Dust and debris particles are one of the most common dangers in the graphic and packaging industry. They can jeopardize the web material when it arrives in your facilities, but they can also be from airborne particles that attach to the web material during different processes.
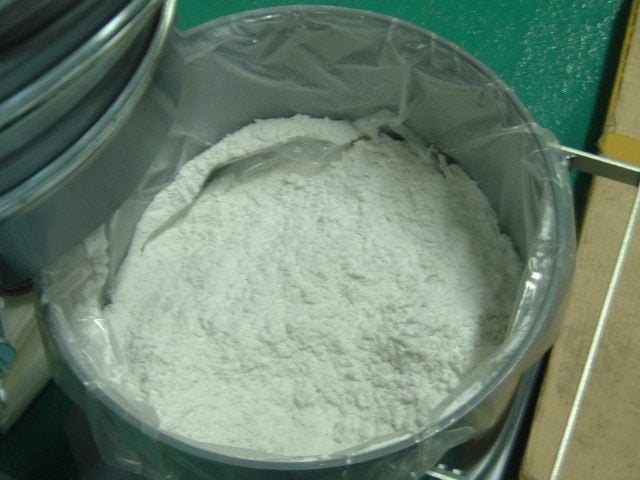
Adhesive Residues
This type of contaminant is often found in industries such as label and packaging production. The adhesive residue from a previous process can attach to the web, contaminating it for the next process. Leaving these contaminants on the material typically causes problems with the bonding quality and further finishing processes (or converting) of the next process in the production.
Lint and Fibers
In the non-woven, textile and glass fiber applications industry, lint and fiber particles are the most common contaminants. These fibers can lead to defects in the subsequent processes.
How Does Contamination Reach the Web Material?
Now that we have discussed the most common contaminants that cause defects or lower the quality of production, we can tell you how the contaminants reach the web material and how to prevent it from happening. First, we explain the different ways in which contamination can happen.
Solid and Corrugated board or Film Particles and Slitting Waste
When cutting, slitting or embossing paper and and board varieties, particles can break away from the film and cause other parts of the same web material to be contaminated with particles.
Pre-contaminated Products
Whenever you receive your product or substrate from a different factory, there is always the possibility that these products are contaminated with dust or debris from the factory of the supplier when they arrive in your facility.
Contamination From the Production Process
In the graphic and packaging industry, processes such as cutting, trimming, and slitting can potentially cause web contamination. For example, the knives or blades that are used during these processes can generate particles and residue, which may be carried onto the web material.
Particles and Dust Attracted by Static Charge
When working with film that is continuously rolling over non-conductive material, there is a possibility that an electric charge gets created within the material. This electric charge works as a magnet for all airborne particles like dust and residue that float around in a factory.
What Are the Advantages of Web Cleaning?
As we have said, the contaminants on web materials or substrates can negatively impact the quality of production. Are you not sure if web cleaning is the best way to go? No problem, we have listed some of the advantages that come as a result of different web cleaning techniques.
Improving Production Quality
Keeping the surface of substrates and web materials clean by removing dust and other contaminants will improve the overall print and finishing quality, resulting in cleaner and more consistent final products.
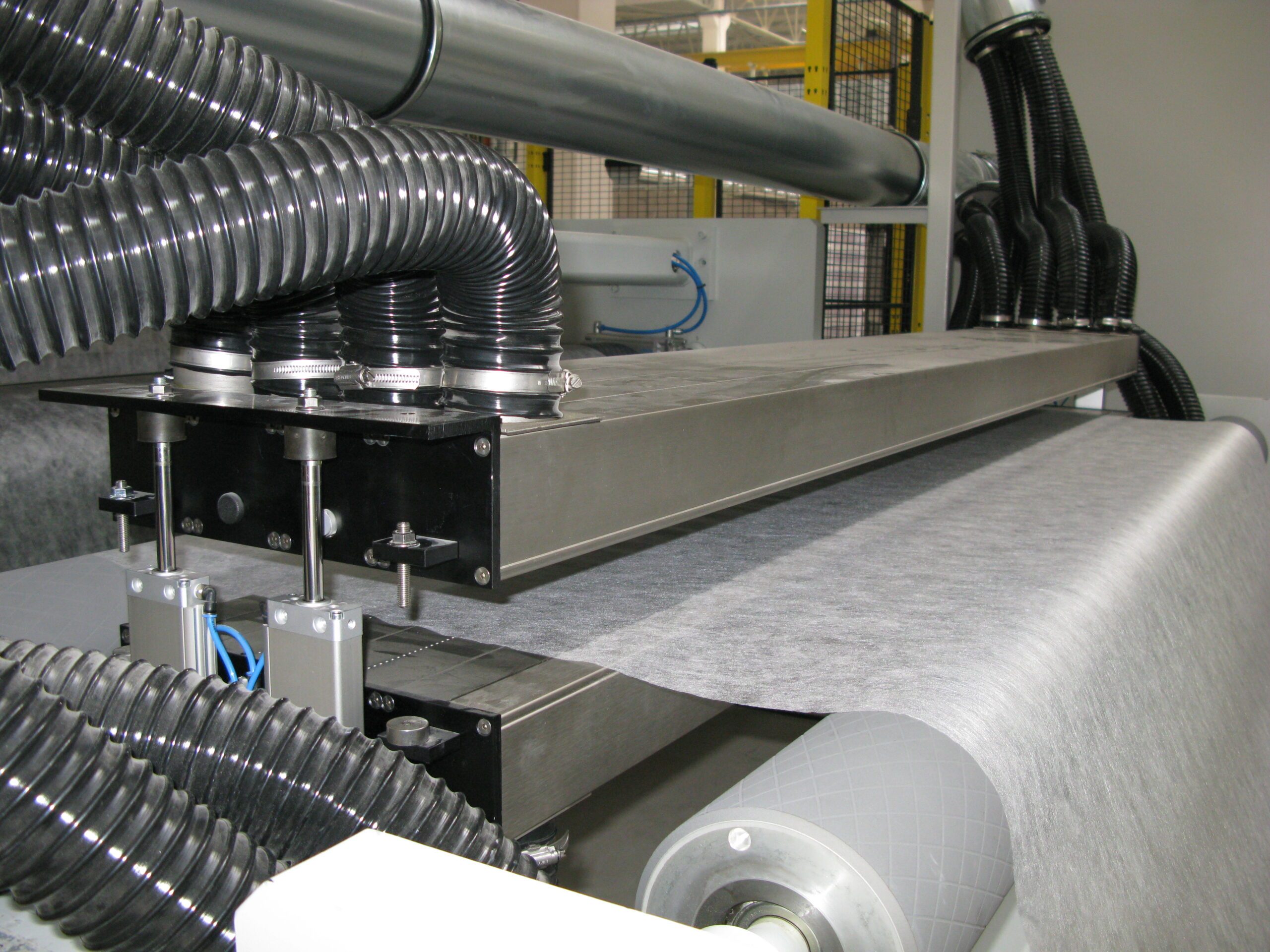
Reducing the Downtime of Machines
Contaminants are not only bad for the web itself. It can also wear down machines. By ensuring that the web that is being used is clean, you will reduce the amount of wear and tear on these, often expensive, machines. This way, the printing, laminating, and converting machines have to be maintained less frequently and can be used for a lot longer. An indirect result of this is that you will end up saving money on the maintenance of the machines and the replacement of machine parts.
Increased Productivity
An indirect result of reducing the downtime of machines by having clean materials or substrates is that the productivity of the machines improves. They can run longer and wear down less often, resulting in an increase in production capacity or increasing the efficiency of these machines!
Creating Less Waste
Whenever a product is not up to standard or does not meet the quality control thresholds, the final product will be rejected and become waste. By investing in good-quality web cleaner materials, you will have fewer defects in your final product, creating less waste. Eventually, this will also help you save money on materials.
High-quality and defect-free final products will result in happier and more satisfied customers. Having satisfied customers can help you build a brand reputation as a trustworthy and high-quality brand.
Customer Satisfaction and Brand Reputation
Why is Effective Dust Removal so Important?
It might not seem like it, but not removing dust or other particles from film or web material can have a significant impact on the quality of the final product. To highlight this, we have listed some reasons why dust removal is so important.
Printing Quality
Dust particles on the printing substrate can interfere with the quality of the printed material. These particles can create defects, streaks, or blemishes on the surface. This will affect the overall appearance of images, graphics, or text.
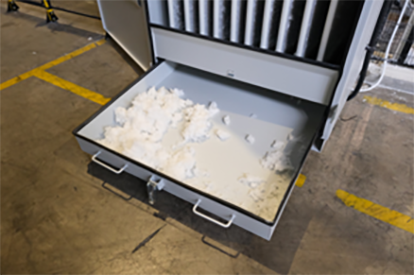
Color Consistency
When printing, even the smallest dust particles can alter the color and cause inconsistencies, which lead to a less uniform-looking final product. This will result in wasted materials and less efficient production processes.
Coating and Lamination
Dust on the substrate in packaging and label production can hinder the bonding quality of coatings, laminates, or adhesives. This can cause poor bonding or delamination, impacting the overall structural integrity of the final product.
Substrate Adhesion
If there are dust particles on your substrate, it can cause problems with the adhesion process of inks and other adhesives. This can lead to label or packaging failure, often causing the need for extra quality control to ensure that the different materials adhere correctly.
Different Types of Web Cleaning
Now that you know why web cleaning is such an essential part of the graphic and packaging industry, we can tell you more about the different types of web cleaning that we offer at Kelva! There are two different types of web cleaning: Contact and non-contact.
Contact Web Cleaning
As the name suggests, with contact web cleaning solutions, the web cleaner will be in contact with either one or both sides of the material. This is a highly effective way to remove contaminants from the materials which have a solid and smooth surface like film, foil, plastic or coated papers. This web cleaner will neutralize the electric charge on the web and remove dust and other airborne particles, so that those cannot attach or settle again.
Non-Contact Web Cleaning
Depending on the material of the substrate and web speed, there is a layer of air carried along by the moving web. The non-contact web cleaners from KELVA are designed to break this layer, release the particles, and then suck them away from the web into the filter. This prevents them from spreading in the surrounding air and reappearing on the film again. The contaminants will be collected in a filter designed to keep them away from the web.
For more sensitive substrates and web materials, non-contact web cleaning is the best option. As the name suggests, there will be no contact with the material. Instead, non-contact web cleaners use powerful air currents to remove and collect dust and other contaminants on substrates.
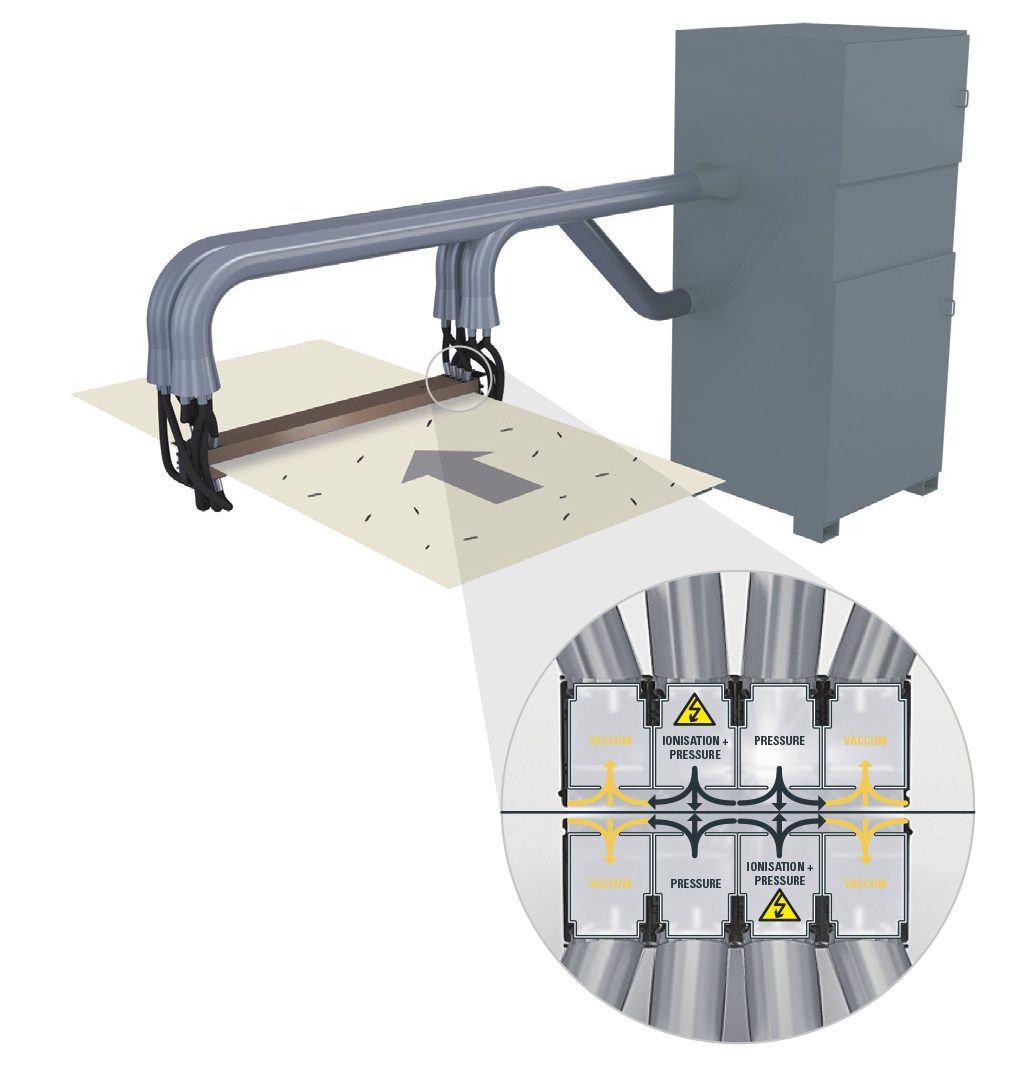
What Parts Does a Non-contact Web Cleaner Consist Of?
A KELVA non-contact web cleaner is built with three main components: A web cleaning head, a filter or fan unit, and a duct system connecting both components. At KELVA the cleaning head used in non-contact web cleaning has integrated antistatic equipment to make sure the electrical charge of the web is removed so that airborne particles will not be attracted to the material again. The duct system guides the removed particles to the filter and fan unit, where they get collected to prevent decontamination of the material and so that these particles can be disposed in a safe manner!
Everything You Need to Know About Web Cleaning With a Non-contact Web Cleaner!
Web cleaning has become an essential part of the production processes in the graphic, packaging industry and other roll-to-roll based industrial applications where materials are processed. It helps with ensuring the highest possible production and finishing quality and quickly saves costs on machine maintenance. Now that you know how web cleaners work, you can find the solution that fits your needs best. KELVA provides contact and non-contact web cleaners for different-sized materials and web widths. Are you not sure what the best solution is in your specific situation? Please don’t hesitate to contact us, and we will help you figure out what the most effective and cost-efficient solution is for you!
contact
Our experts will be happy to help you. Get in touch with us!